top of page

Machinery & Craftsmanship
Take a look behind the scenes and see how we build each ASKT chair—with steady hands, smart tools, and a lot of care.
Precision‑Built, People‑First
From raw steel coil to finished chair in 48 hours—every step filmed, tested and traceable.
From the moment raw steel is cut to the final impact test, every ASKT dining chair traces a fully recorded, ISO 9001-controlled journey that marries millimetre-level precision with a deep respect for the people who craft it. BSCI-audited workshops, body-cam-verified inspections, and 12 in-house test rigs ensure each piece delivers flawless performance—because true quality starts with both engineering rigor and human care.
Line Marking
Every chair starts with visible precision. Our craftsmen use pens to carve reference lines directly into cotton sheets to determine seam allowances, stitch paths and cut points for future upholstery. These permanent guides lock dimensional tolerances to within ±1 millimeter, so every subsequent template, fabric panel, and seam line falls exactly where it's supposed to.


Cotton Planing
Next, a high-density cotton sheet is bonded to the frame to give the seat its first layer of ergonomic contour. Skilled operators “plane” the surface with powered rotary tools, evening out micro-bumps and adding micro-grooves that grip the eventual chair cover. The result is a form-fitting substrate that prevents slip, bunching, or premature fabric wear during years of use.
Template Drafting
Using the original line marks as a map, our pattern engineers create a full-scale plywood template—or “drawing plate.” This master template guides die-cutting for every fabric and foam component, ensuring that each cover wraps the planed cotton perfectly, with no stress points or sagging corners.
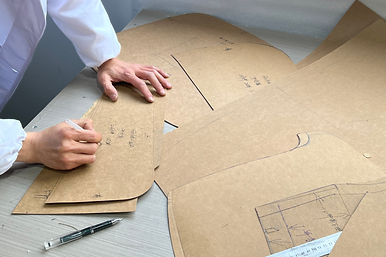
Inside ASKT: How We Build Every Chair with Care
Widget Didn’t Load
Check your internet and refresh this page.
If that doesn’t work, contact us.
bottom of page