How I Evaluate Whether a Dining Chair Is Truly “Good Quality” – A 20-Year Buyer’s Checklist
- Sunbin Qi
- May 22
- 5 min read
As someone who has spent two decades supplying German, Dutch and Swiss retailers with millions of dining chairs, I am asked one question more than any other:
“Sunbin, how can I tell—quickly and reliably—if this dining chair will survive a five-year warranty and still earn five-star reviews?”
Below is the exact 10-point checklist my team and I use inside ASKT and when auditing partner factories. It combines mechanical testing, material science and the nitty-gritty of container loading—because even the strongest chair is worthless if it arrives with a split leg or a failed finish.
1 Start With the Load-Bearing Skeleton, Not the Upholstery
Why it matters:Roughly 70 % of structural failures originate in the frame joints, not in the fabric. Poorly welded or stapled joints loosen invisibly and then break under shock loads.
What I check:
Inspection step | Evidence I expect | Accept / Reject criteria |
Weld profile on metal bases | Continuous bead, no under-cut, TIG/MIG certificate displayed | EN 12520 static load 200 kg passed |
Mortise-and-tenon on solid wood frames | Moisture content 8–12 %, tenon length ≥30 mm | No gaps over 0.2 mm after humidity cycle |
I ask for video of the EN 12520 §6.6 backward-tilt test (20,000 cycles at 37 kg force). If the factory cannot show this footage, I assume the joint design is unverified.
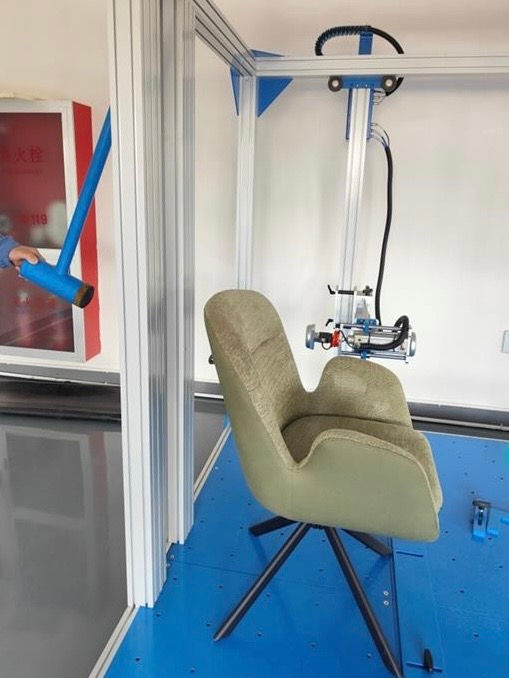
2 Demand Objective Test Reports, Not “Feel-Good” Sit Tests
Europe recognises EN 12520:2020 for domestic seating. North-American buyers use BIFMA X5.4. A credible supplier provides third-party reports—no PDFs, no problem.
Key thresholds:
Static seat load: 1600 N (≈163 kg) for 10 s
Seat impact: 10 kg free-fall from 180 mm, 10 times
Seat/back fatigue: 100,000 cycles at 1200 N/400 N
My own lab in Suzhou repeats the seat impact test on 5 % of every production batch; we reject anything showing >3 mm permanent deformation.

3 Verify Fabric Engineering—not Just Colour Cards
I treat upholstery as engineered textile, not decoration. Three data points decide 90 % of fabric performance:
Martindale abrasion: Minimum 35,000 rubs for residential use, 50,000+ for HoReCa.
Colour fastness to rubbing (ISO 105-X12): Wet ≥ 4, Dry ≥ 4–5.
Pilling resistance (ISO 12945-2): Grade 4 after 2,000 cycles.
For stain-repellent finishes (C0 fluorine-free) I ask for SGS or Intertek reports proving ≥95 % water-oil repellence after five washes. If the supplier claims “pet-friendly,” I ask for ASTM D5587 (tearing) plus a 60-day scratch-simulation video—otherwise it is just marketing.

4 Inspect the Foam Recipe and Density, Not the Thickness
A 50 mm seat cushion can feel luxurious on day one and pancaked on day 90 if the foam is under-spec’d. My rule of thumb:
PU cold-cure foam: ≥45 kg/m³ density
Moulded foam for shells: ≥55 kg/m³, compression set ≤5 % (ASTM D3574)
I request a slice sample during pre-shipment inspection and weigh it with a pocket scale—old-school, yes, but effective.

5 Weight and Balance Tests Catch Hidden Cost-Cutting
An engineered chair has a predictable mass. If a metal-tube chair is suddenly 400 g lighter than the golden sample, somebody has shaved wall thickness or swapped steel for low-carbon ERW. I keep a master database of reference weights; ±3 % triggers an alert.
Tip: Stand behind the chair, hold backrest top, and tilt it toward you. Uneven resistance often signals asymmetrical weld penetration.

6 Surface Finish: More Than Just Gloss Units
Powder-coated steel: Minimum 60 μm film; 500-h salt-spray (neutral) without blistering.
Chrome plating: ISO 1456 Service Condition 3 (≥12 μm nickel + ≥0.25 μm chromium).
Oil-finished oak legs: 2-coat hard-wax oil, 5 % sheen, no fibre raise when wiped with damp cloth.
I carry a dry-film gauge and a simple PTC® cross-hatch knife during factory visits; a 0-2 grid loss out of 100 squares is my pass mark.

7 Ergonomics & Dimensions: The Fast “5-Point Gauge”
Many buyers rely on CAD drawings; I use a folding aluminium jig with five reference lengths that clip together in 30 s:
Seat height 460 mm (±10 mm)
Seat depth 420–450 mm
Backrest angle 100–105°
Backrest height from seat ≥320 mm
Front edge radius ≥25 mm (reduces popliteal pressure)
Why? Because comfort returns & reviews correlate strongly with these anthropometric targets. An elegant chair that forces 90° posture will fail in e-commerce ratings.
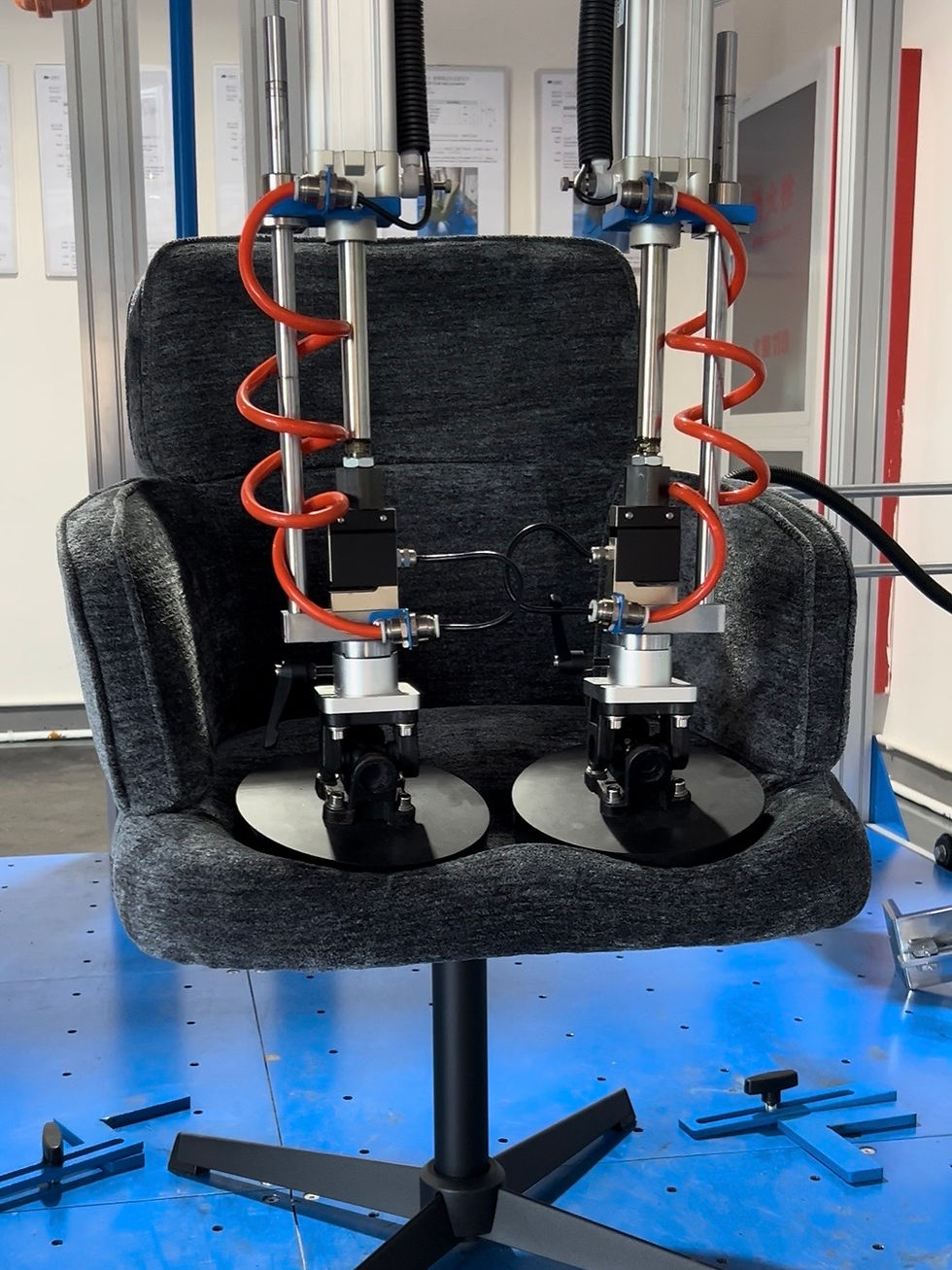
8 Packaging & ISTA-3A Logistics Tests – The Overlooked Profit Drain
A 0.2 % transit damage rate sounds small until you multiply by Amazon’s automatic refund or a retailer’s markdown bin. I audit packaging on four axes:
Honeycomb paper wrap replacing PE foam—cuts EU plastic tax, improves edge crush strength (ECT) by ~15 %.
Inner fixation: Corrugated L-posts + a single paper strap prevent XY-axis slide inside carton.
ISTA 3A drop test: 10 drops from 760 mm on 31 kg package—zero frame exposure, zero leg deformation.
Moisture-sensitive coatings: Use desiccant and 140 g kraft outer for sea-freight to Bremerhaven.
Our switch to plastic-free packs saved German clients ~€0.60 per unit in 2024 plastic taxes.
9 Social and Environmental Audits Are Now Commercial Essentials
European retailers increasingly embed BSCI, ISO 45001 and OEKO-TEX STANDARD 100 into their vendor scorecards. A chair that fails a chemical audit can be quarantined at Hamburg Hafen, tying up cash for 60 days.
I insist on:
Current BSCI audit report with grade C or better.
OEKO-TEX certificates for every fabric SKU—QR codes must resolve to the official database.
Formaldehyde <0.05 mg/m³ (EN 717-1) in plywood seat pans.
Factories that cannot share this data add cost and risk—full stop.
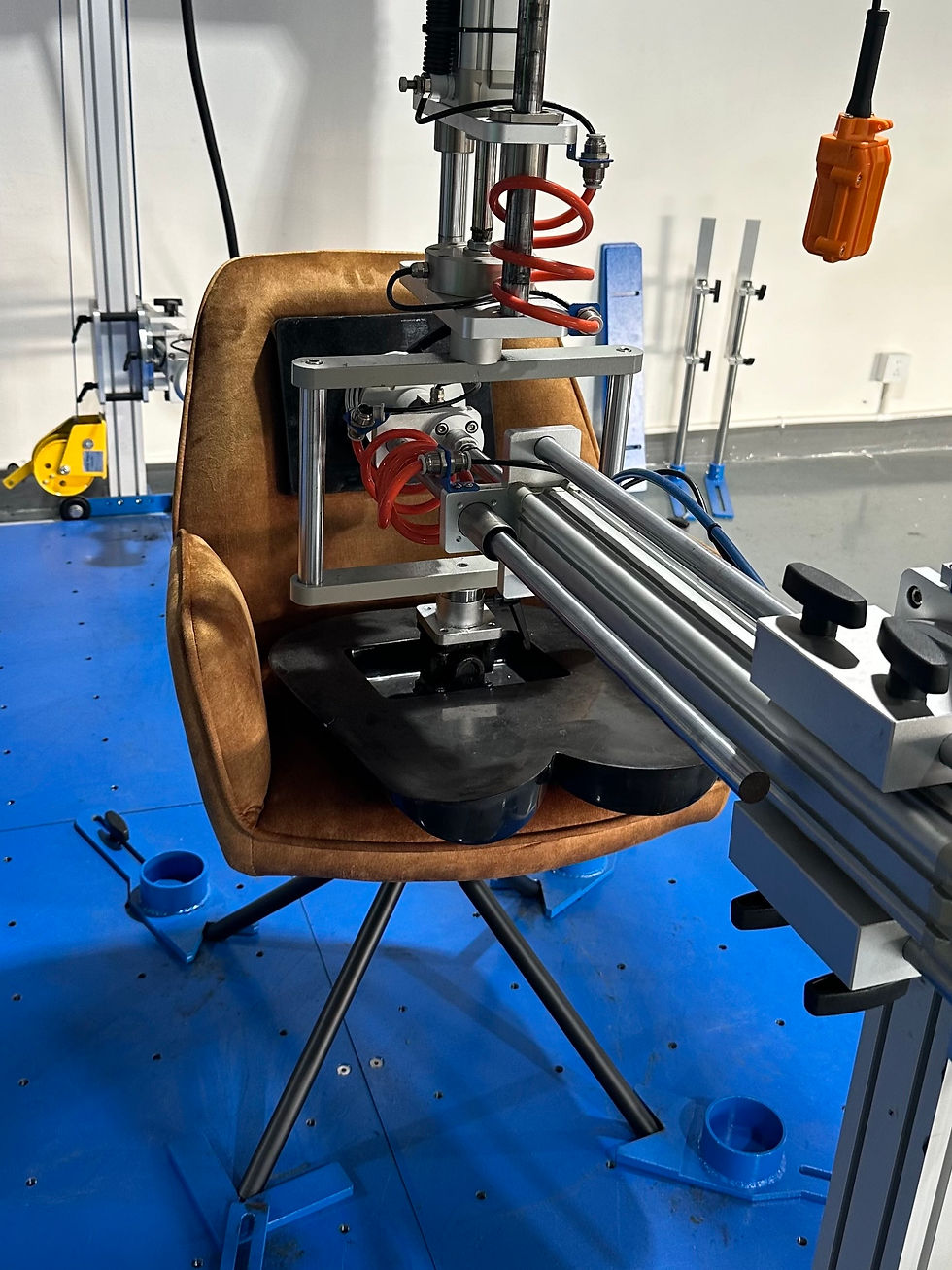
10 After-Sales Playbook: The Hidden KPI Nobody Quantifies—Yet
Quality is not only “MTBF” (mean time between failures). It is also how quickly you can restore quality when things go wrong. My framework:
Metric | Target | Why it matters |
Spare-part lead time | ≤7 days ex-warehouse EU | Retailers avoid full replacement |
QC video traceability | 100 % chairs logged | Identifies root cause in 48 h |
Warranty reserve | 1.5 % of GM | Signals supplier confidence |
At ASKT we barcode every chair and store the EN 12520 video under that code. When a German chain store sends a claim photo, my engineer can watch the exact fatigue test of that serial number within minutes. Resolution = credibility.

Pulling It All Together – My Rapid-Audit Workflow
Desk phase (48 h) – Review standards reports, BSCI, fabric test data.
Lab phase (7 days) – Random sample goes through seat-impact, abrasion and salt-spray in our Suzhou lab.
Factory phase (1 day) – On-site jig measurement, weld inspection, packaging drop test.
Decision – Accept, improve with CAPA (Corrective Action & Preventive Action), or delist.
If you follow these steps, you will catch 95 % of latent defects before the container door closes—and your CFO will notice the drop in returns.
Common Buyer Misconceptions I Still Hear in 2025
Myth | Reality | Evidence |
“Solid wood is always stronger than metal.” | A cold-rolled steel tube with 1.8 mm wall outperforms kiln-dried rubberwood in flexural fatigue. | EN 1729 cyclic bend tests, 100 k cycles. |
“Thicker foam equals comfort.” | Comfort is a function of compression modulus, not thickness alone. | ISO 2439 curves show 35 kg/m³ foam with 5 N cm-2 modulus is softer than 45 kg/m³ at same thickness. |
“I don’t need EN 12520 if I sell online.” | Amazon Germany requires EN 12520 for Category 1006 furniture since 2024. | Amazon Vendor Manual §FUR-01-05. |
Address these misconceptions proactively in your product pages and buyer guides and you will convert faster and suffer fewer post-sale negotiations.

Final Thoughts (and an Invitation)
I have inspected more chairs than most people have eaten hot dinners. Quality leaves footprints. Whether you source from ASKT or another vendor, use the 10-point list above as your roadmap. It compresses 20 years of expensive lessons into one document.
If you need a sample audit template, or wish to benchmark your current supplier against these standards, drop me a line at sales@sinoaskt.com or message me on WhatsApp +86 189 1260 5997. I answer every serious query personally—usually within one European business day.
Let’s make sure the next container you receive is filled with chairs that stay sold, not returned.
— Sunbin Qi, CEO, ASKT Furniture
Comments